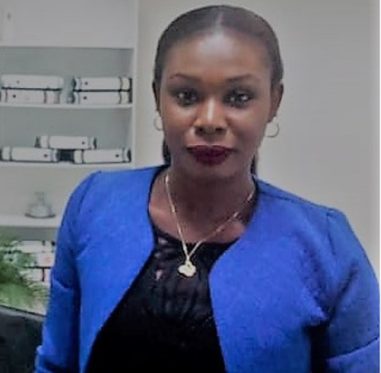
Nancy Freeborn is the Project Head, Women Empowerment Programme Scheme Synergy (WEPSS), a Corporate Social Responsibility Project of Nigeria’s oil and gas logistics giant, INTELS Nigeria Limited. In this interview, Freeborn speaks on the impact of the project on Nigerian women, especially those in the Niger Delta region.
WEPSS clocked five recently. Would you say its objectives have been achieved?
Yes, they have. This centre was set up in 2013 to empower community women in host communities where INTELS operates. It is a corporate social responsibility of INTELS, so it is their way of giving back to their host communities and the Niger Delta at large. The goal from the beginning was to empower 5,000 women over a 20-year period through the acquisition of tailoring skills. So far, we have been able to empower more than 1,000 women, and I would say we are doing great. We try to reach out to people from the grassroots so we go into the communities so that those who really need this skill can apply. Our criteria are that you don’t need so much education. Just be able to read and write. It is like coming from the farm to factory; these are the people we are looking to empower. Every year, we have two training sessions, which last for four and a half months each. The age range for the trainees is between 17 to 45 years. Prior to this time, we used to take in 50 trainees per session; that is 100 trainees in a year. Currently we take a minimum of 200 trainees every year and that has been ongoing for some years now.
The day to day running of WEPSS is solely funded by INTELS, down to the smallest needle and the materials we use to train our students. Once the trainees come to WEPSS, they are not only taught the practical aspects of tailoring, there are some theoretical aspects, which they learn. For example, a common part of tailoring that is popping up lately is garment illustration and how to sketch fashion figures. We teach them that here and the basics of sewing; how to use a measuring tape and even get them to run on paper before they begin to sew on actual fabric. The women are taught machine handling; they learn how to use different specialized machines. They are able to sew four basic garments; cut and sew before they leave here. The kind of training our trainees receive here is comparable to international standards. They also get soft skill training on personal hygiene, how to handle their business better when they leave here, social ethics and responsibility. When some of them come here, the way they dress and look isn’t good but at the end of the training, they leave as distinguished ladies who know how to carry themselves. This is because we take the extra time to teach them how to carry themselves. If you do not represent your brand well as a tailor, people will not come and make clothes with you. You have to make nice looking clothes for me to be interested; that is where it starts. When the women have completed their training, we still keep in touch through regular follow-ups. Anytime there is a graduation ceremony, we invite our alumni to come over. We know the progress that they have made and we know who to invite and who to showcase.
How would you describe WEPSS’s journey till date?
As one of the members of the pioneer set, I got to see this place grow. I came in 2013 as a trainee. At the time we started, this place was practically under construction. I have seen it evolve and grow from being a little training centre to a garment manufacturing factory and then back to a training centre again. About 300 rural women were taken in the pioneer set for the training. We came in several batches because we were many in number. We were trained and retained, all 300 of us, as factory hands to work in our garment producing factory here. Back then, we produced as much as 300 garments daily. These garments – for instance coveralls – were being produced for companies at the Onne Oil and Gas Free Zone. Most of my trainers and cutters were also part of those 300 rural women. When this project started, we were being trained by Indians and Italians. We had a consultant from India. They came, introduced the program to us and left when they were done. INTELS ensured that the knowledge was handed down from the expatriates to us; it is now a core community project because it is handled by people who are from the Niger Delta region. After I was through with my training; my performance was very good so I had more opportunities for growth. I started as a trainee, became a trainer, then head trainer, production supervisor, head production supervisor, before I finally became project head. I have learned so much in the process. Every other person you see working at the WEPSS centre was trained here including the technicians. INTELS has not just only given to the trainees who come here for four and a half months but also to the people who work here.
What has your experience as WEPSS Project Head been like?
I have worked here as Project Head for seven months. It has been fun; it is just added responsibility, which is fun to handle. It has its ups and downs but that is the beauty of life. Every batch of trainees comes with its own peculiarities. Some come here very heady but at the end of the day, we still get them to learn and they leave here happy. At the end of the day, the training is about moulding them in character and in learning. With this particular set of trainees, the biggest challenge was their dressing because we had so many young girls among them. You tell them not to wear something, the very next day; they will do that exact same thing. It was pretty challenging getting them to understand that they were no longer children but ladies who have to carry themselves in such a manner that they can handle a business of their own when they are done with this training.
How many sets of trainees has WEPSS graduated since its inception?
A total of six; the second set for 2018 graduated a few weeks ago. This set just like the one before it, was very competitive. We have this star chart we create for every assessment; there is a trainee who is the star of that assessment. We can tell how competitive each set has been by looking at how many times a trainee gets to appear as a star on the chart. In this set, we had just one person appear more than once. The rest were knocked off after just one appearance. The best graduating trainee in this last set is 18 years old but we have had a winner in the past that was younger than her. I noticed that this time around we had a lot of young trainees. Perhaps it is the success of the project that is attracting young women from their various communities to WEPSS. They get to hear of other women who have acquired the skill and are able to do something with it. So many young girls who ordinarily would not have considered the program as something they want to do, are now interested in getting the skill.
When our trainees leave here, it doesn’t end there. We keep in touch with them to know how they are doing; we always find a couple of them using the skills to better their lives. A few of the WEPSS alumni came for the last graduation ceremony. I am particularly excited about one of them who graduated in 2017 because she now sews Ankara shoes, bags and accessories with the help of the sewing machine she was given by INTELS. Most of the women would normally focus on clothes but she decided to do something very different. We have also received requests from other fashion designers who ask for some of our trainees to come work for them when they graduate. A friend of mine contacted me recently about starting a garment factory that would produce men’s shirts in Rivers State. He was asking to see if he could hire some of the women here when they complete their training. When such opportunities come, we make them open to our trainees. The younger trainees might still have some aspirations; we don’t discourage them from aspiring for other things but we always encourage them to use the skills they have acquired from WEPSS. Some of them might want to further their education but they don’t have the funds. However, having being trained on fashion designing and tailoring, they can use the skills to fund their education.
Copyright Ships & Ports Ltd. Permission to use quotations from this article is granted subject to appropriate credit given to www.shipsandports.com.ng as the source.