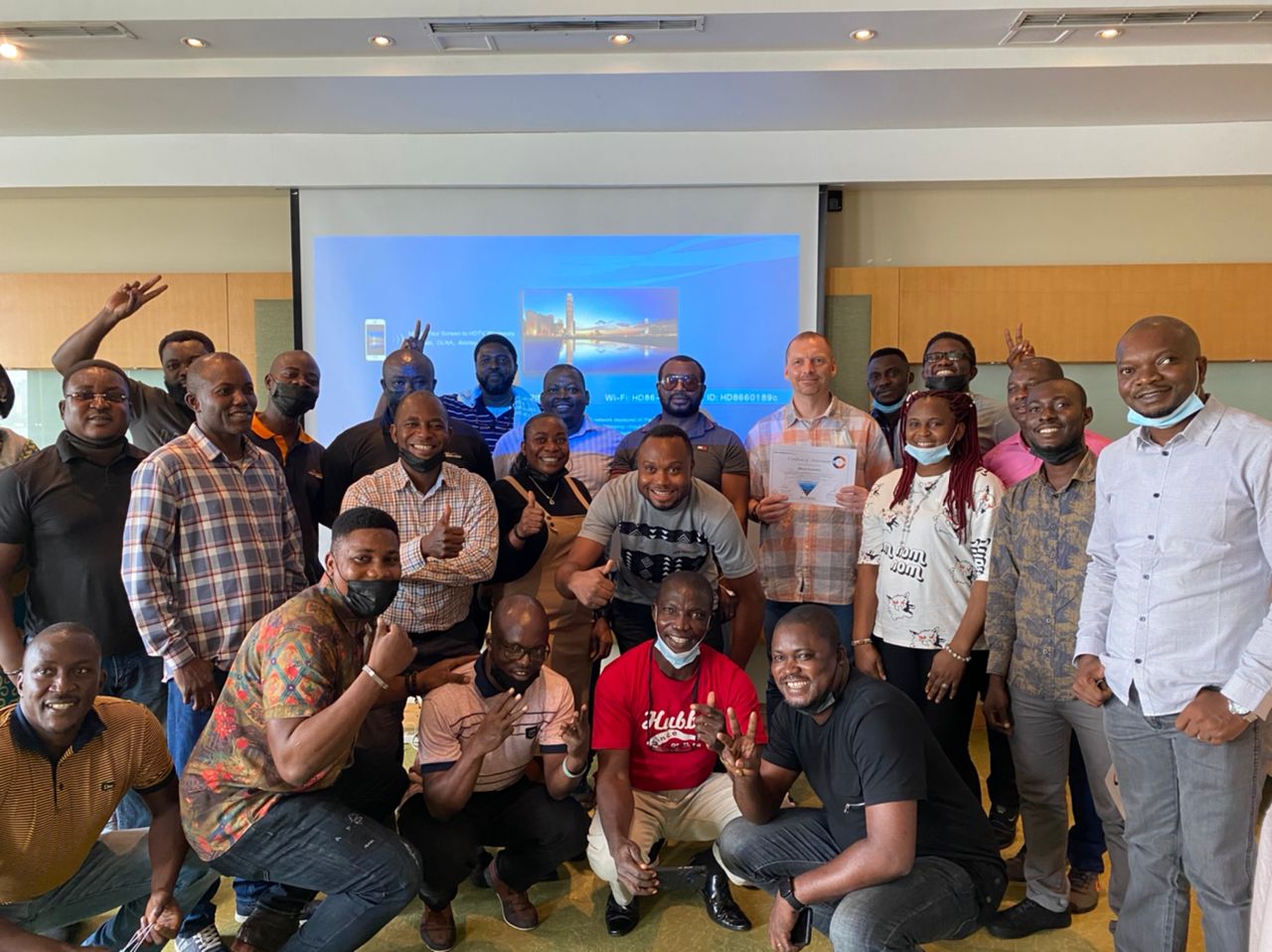
APM Terminals Apapa said 175 of its employees have graduated as “lean practitioners” since the company started its Lean Academy in 2019.
Coined by James Womack and Daniel Jones, “lean” is a way of thinking about creating needed value with fewer resources and less waste. It is based on Toyota’s fabled Toyota Production System – The Toyota Way, which provides a set of principles and behaviours that underlie the Toyota Motor Corporation’s managerial approach and production system.
Toyota first summed up its philosophy, values, and manufacturing ideals in 2001, calling it “The Toyota Way 2001”. It consists of principles in two key areas: continuous improvement and respect for people.
The Toyota Way has been designated “a framework intended to give the instruments to individuals to constantly improve their work”.
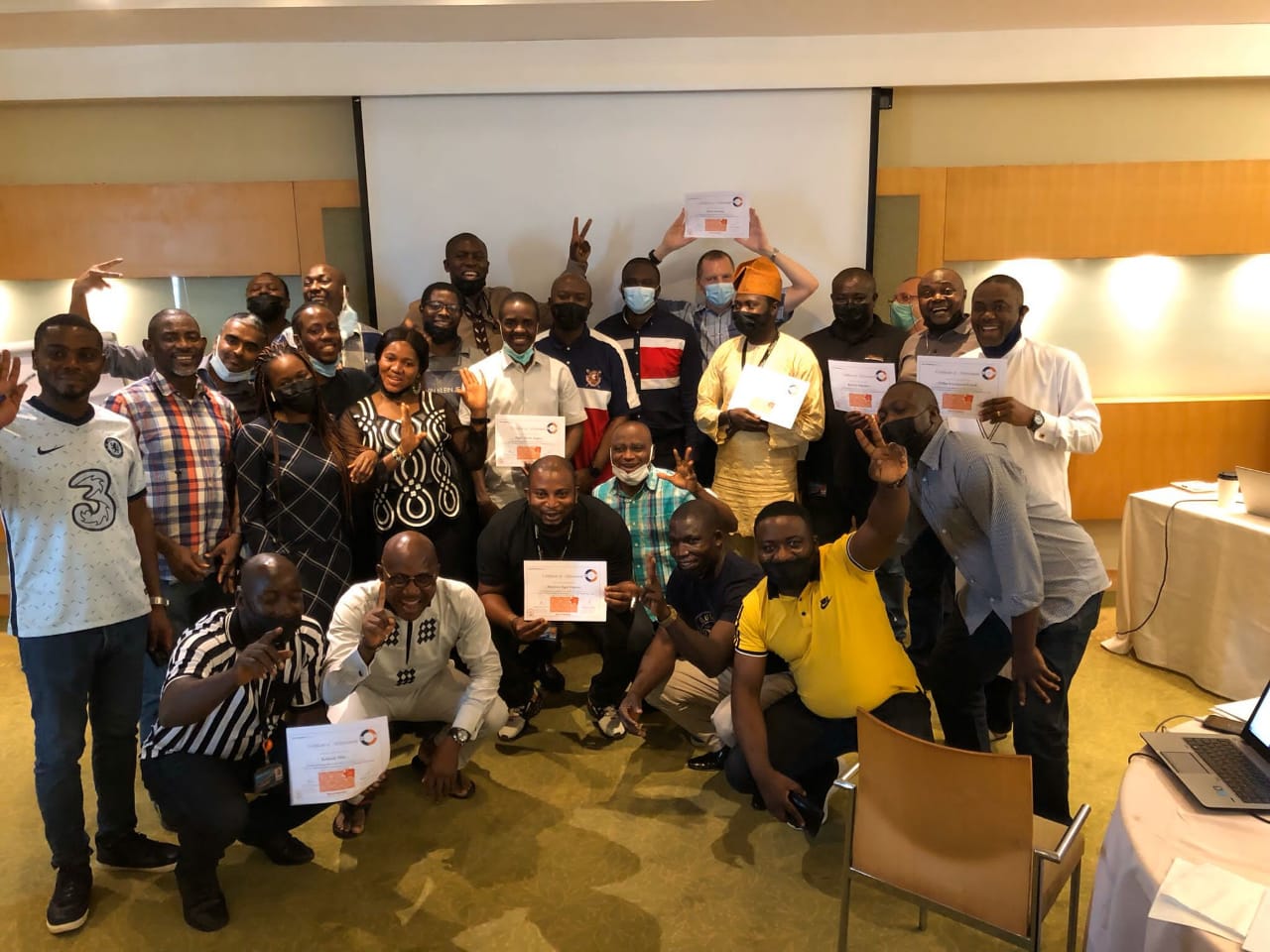
In a statement issued weekend, APM Terminals Apapa said the lean practitioners are expected to take the lead in introducing innovative solutions to terminal operations with the goal of improving efficiency and customer service.
It said APM Terminals Apapa is transformed by retooling and reeducating employees to eliminate waste, boost productivity and promote innovation.
Commenting, APM Terminals Way of Working (WoW) Project Manager, Martin Kjeldsen, said, “Our employees play a central role in our transformation. They are the ones who will make Apapa a great place to work through involvement and engagement within our Way of Working, through high level of lean education, a lean mindset and Kaizens – for immediate, real results and long-term sustainable impact.”
Kaizen is a Sino-Japanese word for “improvement”. It is a concept referring to business activities that continuously improve all functions and involve all employees from the CEO to the assembly line workers. Kaizen also applies to processes, such as purchasing and logistics, that cross organisational boundaries into the supply chain. It has been applied in healthcare, psychotherapy, life coaching, government, and banking.
He said in the past years, the terminal worked extensively on identification of talent at Apapa to support the future lean journey and building relations within the Apapa team to ensure cross functional collaboration.

“Practicing lean requires a changed mindset from running the business to improving the business, helping us preventing fire-fighting in our day-to-day job. It’s not easy, but it is manageable if we set our minds to it. If we invest heavily in WoW and celebrate our successes,” Kjeldsen said.
Also commenting, another Way of Working (WoW) Project Manager, Jan Jensen, said, “The end of 2021 showed that we are on the right lean path in Apapa. Lean training and coaching are now showing more engagement and more willing to learn how to use the lean tools to improve our daily work-life balance. We are beginning to see the result around the terminal where employees start and execute their own team Kaizens to improve their processes and the way they perform their daily work.”
A major milestone in the terminal’s Lean journey is the introduction of practical WoW coaches. This is a dedicated stand-alone role with the objective of strengthening APM Terminals Apapa’s lean capabilities and knowledge of WoW tools.
A practical WoW coach, Victor Enegide, said, “To us, as employees, it gives a better understanding of what we do on a day-to-day basis. It also makes us understand that we shouldn’t let good get in the way of better. Its benefit to operation is the elimination of waste, improvement of truck turnaround time and better customer satisfaction. It also reduces bottlenecks to enable the process flow easily.”
Copyright Ships & Ports Ltd. Permission to use quotations from this article is granted subject to appropriate credit given to www.shipsandports.com.ng as the source.